Plastic granule machine is the key equipment for plastic waste regeneration. Its performance and design play a vital role in the whole regeneration process. Some people put forward the idea of designing the plastic dana making machine into wet and dry, however, in the actual application of wet and dry granules making machines are faced with a number of difficulties.
Plastic granule machine material handling differences
There is a clear difference in the working principle and material handling between dry and wet plastic dana making machines. Dry granules making machines are suitable for dry waste plastics, while wet plastic granule machines require the addition of binders or liquid components. Combining the two may complicate the workflow and make it difficult to meet the requirements of both dry and wet processing, thus affecting the granulation effect.
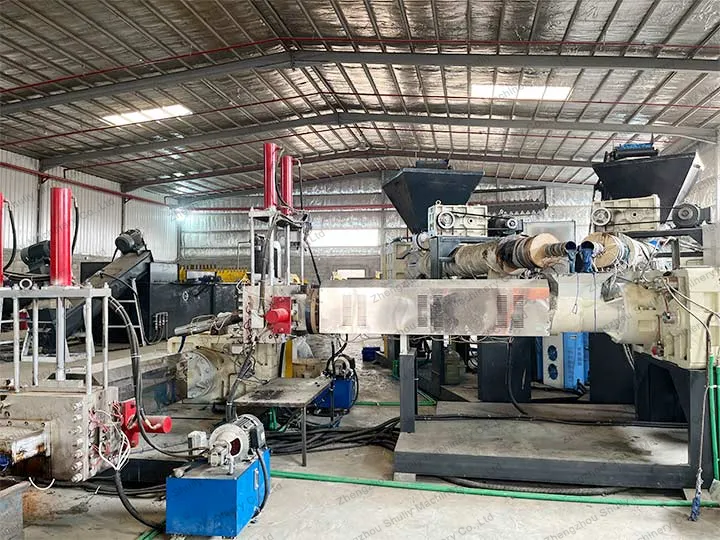
Granules making machine structure is different
Due to the difference in process principles between dry and wet granulation, the corresponding plastic granule machines will differ greatly in structural design. Dry granules making machines usually need to have extrusion and compression to ensure the formation of dry particles. Wet granules making machines, on the other hand, need to be equipped with mixing and wetting functions to ensure that the liquid components and binders are fully integrated. Therefore, to realize both wet and dry functions on the same plastic dana making machine requires complex structural design and functional configuration, which increases the manufacturing cost and difficulty.

Plastic granule machine process is different
Dry and wet plastic granule machines have different process parameters and different requirements for material handling and particle formation. Designing a plastic dana making machine for dry and wet pelletizing may result in a compromise between the two processes. This can result in unstable pellet quality. The quality and performance of recycled plastic can be seriously affected.
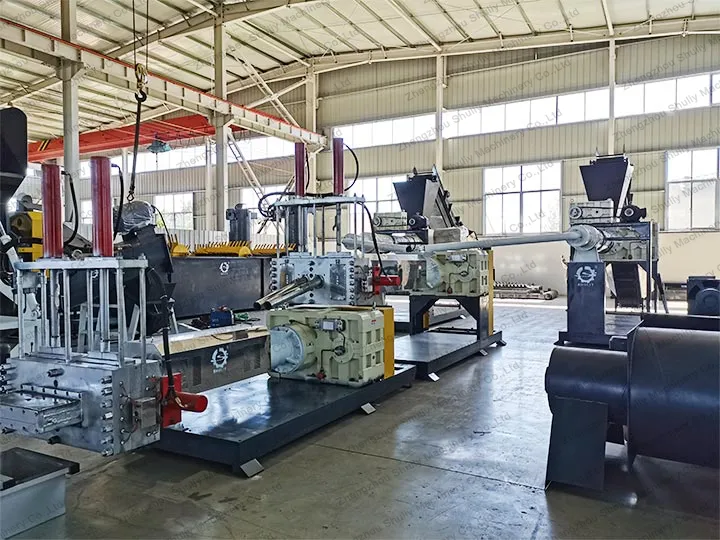