As the two main processes in plastics granulators, dry granulators and wet granulators provide an effective solution for plastic waste regeneration. This paper will introduce and compare the dry granulator and wet granulator. It aims to provide a reference for choosing a suitable granulator.
What is dry granulator and wet granulator?
Dry granulators and wet granulators are both plastics granulators used to convert raw materials into granules. Dry granulation takes solid raw materials and makes them directly into pellets through processes such as drying and compression, without the addition of liquid. Wet granulation suspends the raw material in a liquid. A binder is added through wet processing and then dried to form granules.
Dry granulation is suitable for materials that are not resistant to moisture and for large-scale production. Wet granulation is suitable for scenarios with high demands on granule characteristics and quality.
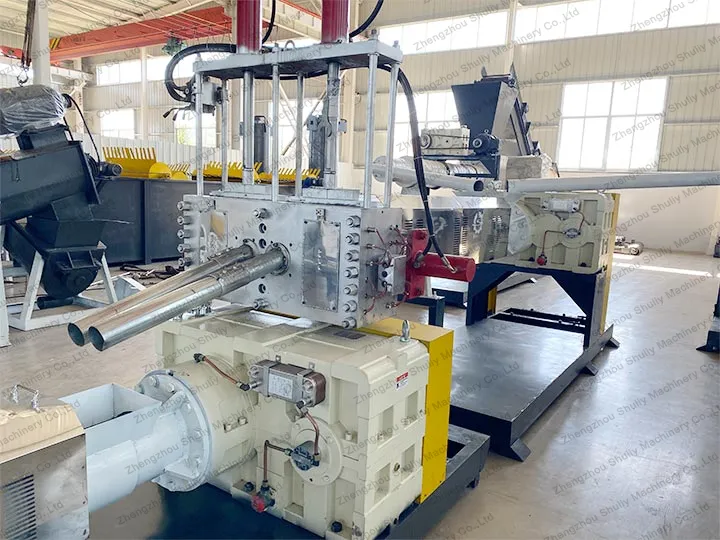
How to choose between dry granulators and wet granulators?
When choosing between dry or wet pelletizing, the following factors need to be considered to determine the most appropriate type of plastics granulator:
- Raw material characteristics: First of all, we should understand the nature of the raw material, including its physical properties, humidity requirements, and whether it is resistant to moisture. If the raw material is sensitive to humidity, a wet granulator may be more suitable; while for the raw material that is not resistant to moisture, a dry granulator may be more suitable.
- Product requirements: Consider the requirements of the end product, including characteristics such as particle size, shape, and density. Wet granulation generally allows for more precise control of particle characteristics and is suitable for scenarios where product quality is required.
- Production scale: Select the appropriate type of plastics granulator according to the expected production volume. Wet granulators are generally suitable for smaller-scale production, while dry granulators have advantages in large-scale continuous production.
- Cost considerations: Consider the cost of purchasing, operating, and maintaining the equipment. Typically, dry granulators have lower energy and maintenance costs, but this depends on the equipment type and production scale.
- Process flow: Take the entire production process into consideration, including the pre-treatment of raw materials and subsequent processing. Make sure that the plastics granulator you choose is compatible with the entire process.
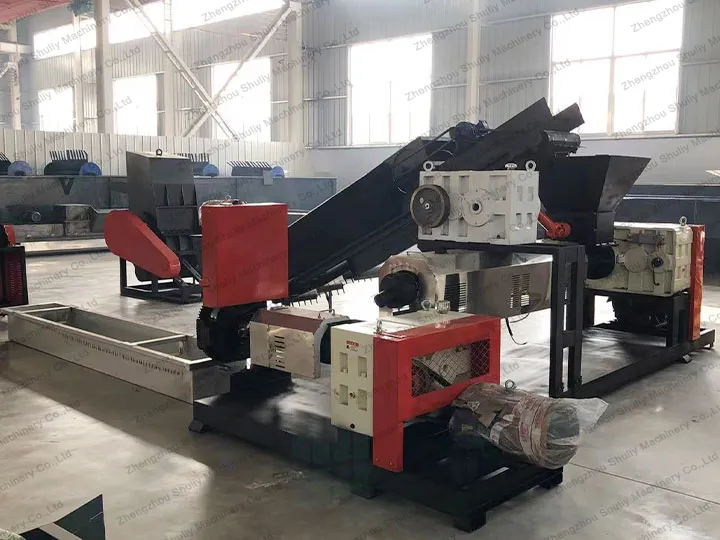
In summary, the choice of dry granulator or wet granulator should take into account the characteristics of raw materials, product requirements, production scale, cost and process, and other factors. Ensure that the final choice of plastics granulator can meet the production requirements and obtain better economic benefits.
For more information about plastics granulator, please visit our official website https://shuliypre.com/
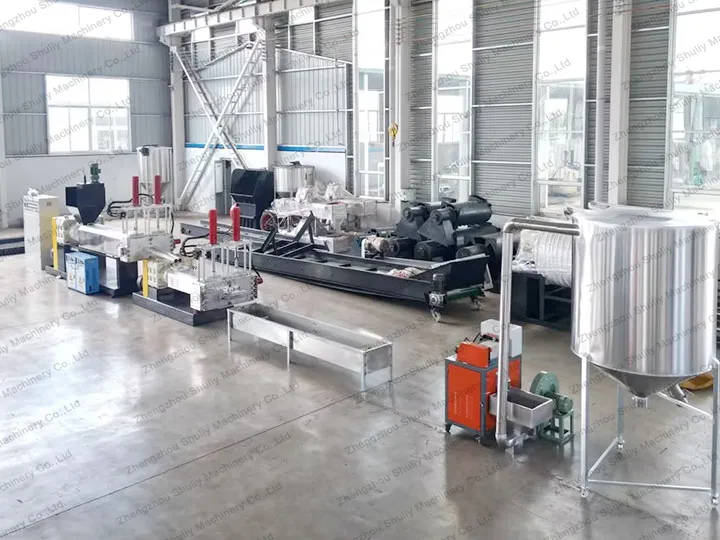