Industry plastic granulators can heat and melt the waste plastics, and then make them into plastic granules through extrusion, cutting, and other processes. Temperature is one of the important factors affecting the plastic pelletizing process. If you want your plastic granules to be competitive in the market you must control the temperature of the pelletizer equipment.
Effect of industry plastic granulator temperature on plastic melting
In the plastic pelletizing process, the plastic first needs to be heated and melted. The temperature of the industry plastic granulator directly affects the movement speed of the plastic molecular chain and the degree of melting. Too high a temperature in the pelletizing recycling machine will cause the plastic to decompose, producing odors and harmful substances, thus reducing the quality of the plastic pellets. While the pelletizer equipment temperature is too low may make the plastic fail to melt completely, affecting the appearance and physical properties of plastic granules.
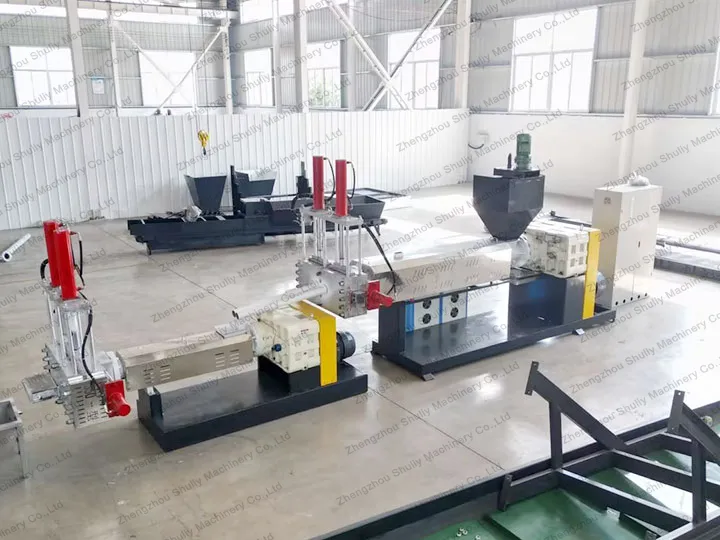
Hardness of plastic pellets and temperature of pelletizer equipment
The regulation of the temperature of the industry plastic granulator also affects the density and hardness of the plastic granules. The pelletizing recycling machine temperature is too high will make the plastic particles thin, and density decreased. Too low a temperature will make the particles thicker, density increased. In addition, the temperature of the plastic pelletizing machine also affects the cooling speed of plastic particles, which in turn affects the hardness of the particles. Reasonable adjustment of the temperature of the pelletizer equipment can obtain a stable quality of plastic granules.
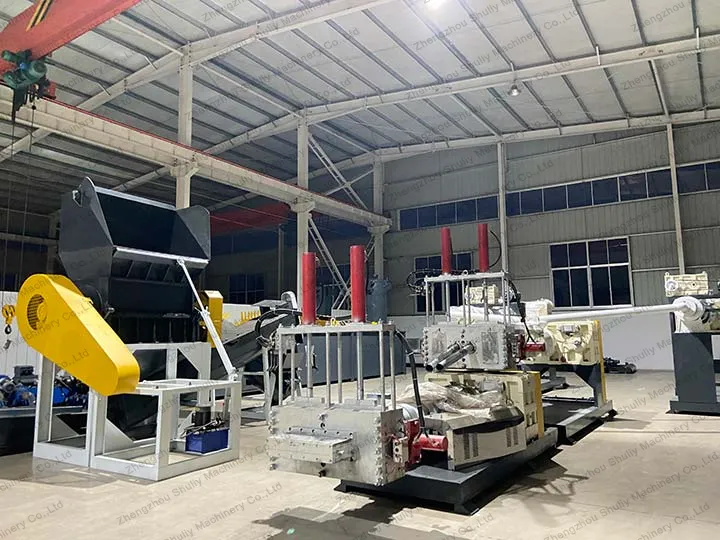
Temperature control of an industry plastic granulator is critical to the quality of plastic pellets. Proper temperature regulation can improve the quality and output of plastic pellets and bring us higher profits.
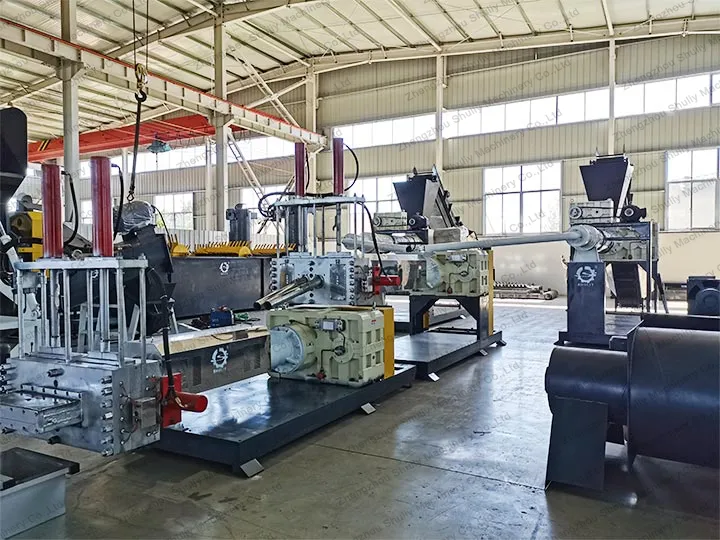