Plastic pellets produced by PVC extruders appear hollow, which may affect their quality and applicability. Has your pellet granulator ever produced hollow plastic pellets? Are you suffering from this problem? Today, in this article, we’ll discuss the reasons why this happens and how you can get your PE granulating machine to produce higher-quality plastic pellets.
High moisture content of PVC extruder raw material
Too high a moisture content in the raw material entering the PVC extruder is a major factor in the hollowing out of plastic pellets. High moisture content creates steam during the pelletizing process in the pellet granulator, which prevents proper plasticization of the plastic. Steam expansion can cause voids to form inside the plastic granules, resulting in hollow plastic pellets. Therefore, it is important to ensure that the moisture content meets production requirements before the raw material enters the PE granulating machine. We recommend incorporating a plastic dryer machine into the plastic pelletizing line to dry the raw material efficiently.
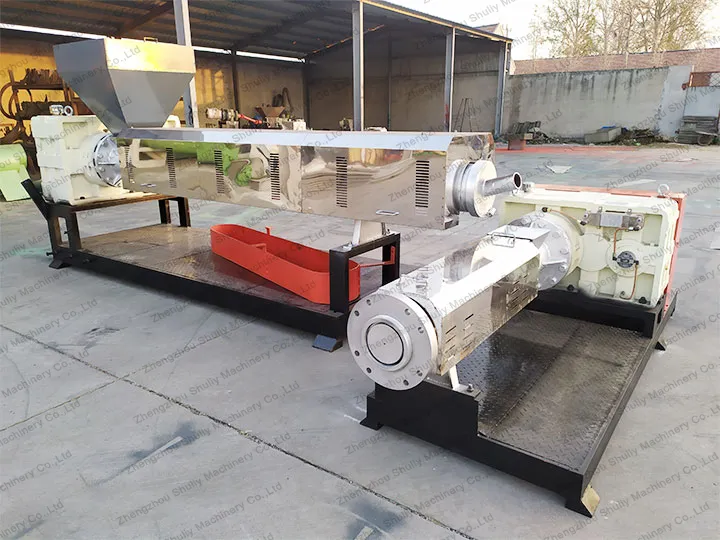
Temperature of pellet granulator
The temperature of the PVC extruder is critical to the plasticizing process. If the temperature of the pellet granulator is too low, the waste plastic cannot be fully plasticized. This can result in the presence of unmelted areas within the plastic granule. These unmelted areas may create voids during the cooling and curing process, resulting in hollow plastic pellets. Therefore, it is important to ensure that the temperature of the pe granulating machine meets the production requirements during the production process to ensure that the plastic is fully plasticized.
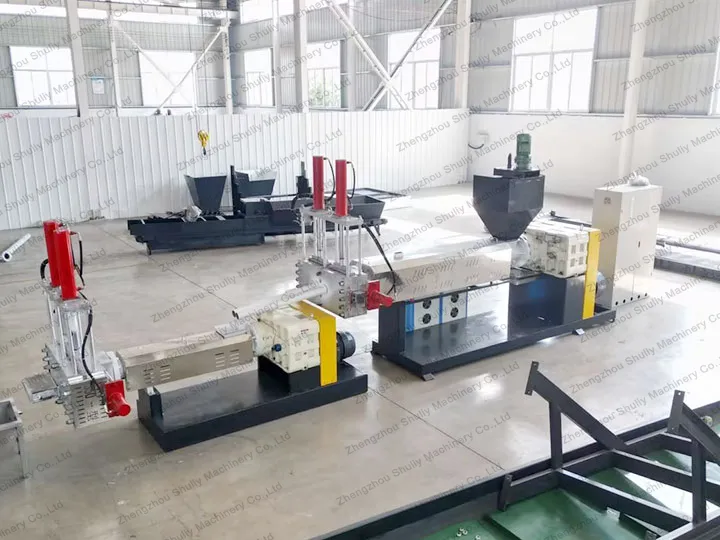
Cooling tank temperature is too low
In a plastic pelletizing line, the cooling tank is located after the PVC extruder. Its main function is to effectively cool the plastic after it comes out of the PE granulating machine to ensure that the shape and quality of the plastic pellets remain stable. If the water temperature in the cooling bath is too low, the plastic granules will cool too quickly. This can cause the outer layer of the plastic pellet to solidify while the interior remains fluid. This can cause voids and shrinkage inside the plastic pellet. Therefore, it is important to ensure proper water temperature during the cooling process to avoid the problem of hollowing plastic granules.
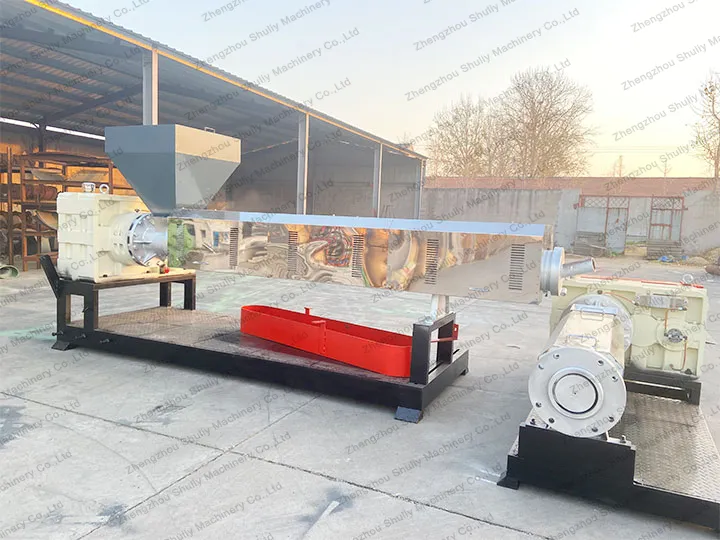
The appearance of voids in plastic pellets produced by a PVC extruder is usually related to factors such as the moisture content of the raw material, the temperature of the pellet granulator, and the cooling temperature. All of these factors affect the plasticizing and curing process of the plastic, resulting in voids and shrinkage within the pellets. In order to solve this problem, we need to strictly control the machine temperature and raw material moisture content during the pelletizing process of the PVC extruder.